Our Product
Elmo Rietschle
Central Compressor Series

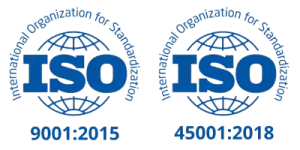
Advanced at a glance
The medical air system and/or instrument air system is a set of equipment consisting of an oil-free compressor, air dryer, filters, tank, dew point and CO monitor, pressure regulator, and control panel, used as a power source for medical instruments and respiratory medical devices, as well as for medical and instrument air.
How a Medical and Instrument Air System Works
Air Intake
The system draws in ambient air through the oil-free compressor. Using an oil-free compressor ensures the air is clean and free from oil contamination, which is critical for patient safety and the function of medical instruments.
Compression
The air is compressed to a required pressure level. Since it’s oil-free, there is no oil mixed in with the air during this process.
Cooling
After compression, the air is usually warm. It passes through a cooler or heat exchanger to reduce the temperature before the next stage.
Air Drying
The air dryer removes moisture from the compressed air. This is important to prevent condensation and microbial growth in the piping and medical devices.
Filtration
The dried air is then passed through several filters to remove particles, bacteria, and any remaining impurities.
Monitoring
The system continuously monitors:
- Dew Point – to ensure the air stays dry
- Carbon Monoxide (CO) – to ensure patient safety from toxic gases
Storage in Air Tank
The clean, dry, and safe compressed air is stored in a pressurized tank. This ensures a steady and reliable air supply during peak usage or power interruptions.
Pressure Regulation
Before being delivered to medical equipment or respirators, the air passes through a pressure regulator to ensure consistent and safe pressure levels.
Control Panel Operation
The entire process is managed and monitored via a control panel, which allows operators to adjust settings, view system status, and respond to alerts.
Delivery to End-Use
Finally, the medical-grade compressed air is distributed through the hospital or clinic’s pipeline to respiratory equipment, surgical tools, dental units, ICU systems, and other medical devices.
Technical Features of a Medical and Instrument Air System
-
Oil-Free Compressor (Non-Lubricated Type)
-
100% oil-free operation to prevent contamination
-
Scroll or piston type, designed for medical use
-
Low vibration and noise levels (suitable for hospital environments)
-
-
High-Efficiency Air Dryer
-
Refrigerant or desiccant type
-
Removes moisture to maintain dew point as low as -40°C or better
-
Prevents microbial growth and condensation
-
-
Multi-Stage Filtration System
-
Pre-filter, bacterial filter, and final filter
-
Particle retention down to 0.01 micron
-
Filter efficiency ≥ 99.9999%
-
Complies with ISO 8573-1 Class 1.1.1 (or equivalent)
-
-
Dew Point & CO Monitor
-
Continuous monitoring of air dryness and carbon monoxide concentration
-
Alarm system if levels exceed safe limits
-
Data logging capability for regulatory compliance
-
-
Air Receiver Tank
-
Made of anti-corrosive material or internal coating
-
Designed to handle medical-grade compressed air
-
Equipped with pressure relief valve and drain valve
-
-
Pressure Regulation System
-
Stable and adjustable outlet pressure
-
Dual regulation for different applications (instrument use vs. respiratory use)
-
-
Automatic Control Panel
-
PLC-based smart control
-
Real-time display of system parameters (pressure, flow rate, dew point, CO level, etc.)
-
Alarm system with visual and audible indicators
-
Remote monitoring capability (optional)
-
-
Redundancy & Backup
-
N+1 configuration (redundant compressors/dryers)
-
Ensures continuous operation during maintenance or failure
-
Automatic switch-over between units
-
-
Low Noise Operation
-
Noise level typically < 65 dB(A)
-
Enclosed design for installation near patient areas
-
-
Compliance & Certification
-
ISO9001:2015
- ISO45001:2018